Since the end of September we are recertified according to ISO 9001:2015. In this article we would like to give you an insight into the certification process and show how we are constantly improving for our customers.
Inhalte
The decision to improve processes was easy for us
The decision to certify the company according to ISO 9001 was made as early as 1997 and was largely based on the desire to increase competitiveness through a recognized seal of quality. The company’s core processes, most of which were already documented or clearly anchored in the minds of the employees, were to be certified and recorded in a separate quality manual.
An additional motivation was the potential for ongoing and structured improvement of processes and documentation, as well as the increased ability to communicate strategically important fundamentals, such as the corporate mission statement.
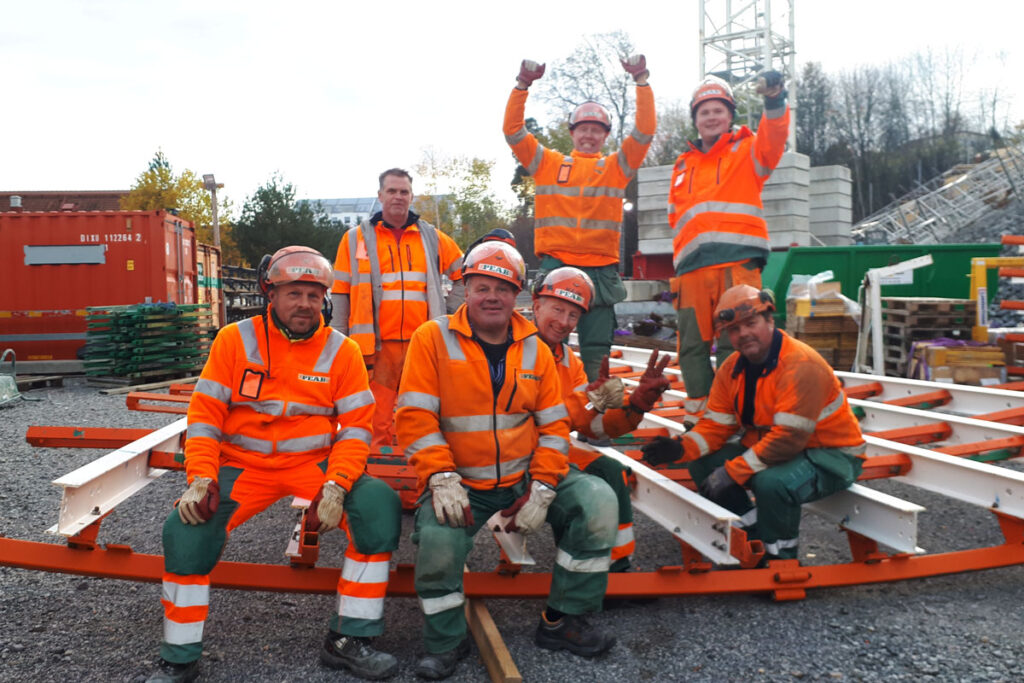
Due to the revision of ISO 9001 (2015), which focuses less on strict documentation requirements and more on a living quality management system, as well as the introduction of a new ERP system (Enterprise-Resource-Planning) for the company, we also had the opportunity to update or revise existing documentation and company processes.
In 2020, another major effort was then made and parts of the QA system were fundamentally revised. Great importance was attached to the structure and organization of the system in accordance with ISO 9001:2015.
The audit
At 23. and September 24, the 8th repeat audit took place. The audit was conducted by auditor(s) of TÜV SÜD Group on the basis of the audit principles.
The basic objectives of the audit were review and evaluation:
- the conformity of the management system with the audit basis(s)
- the ability of the management system to meet applicable legal, regulatory and contractual requirements (binding obligations)
- of the effectiveness of the management system and the framework for possible improvements to the management system.
- the suitability of the management system to meet the defined objectives on a sustained basis
No deviations were found and the following positive comments were made by the auditors, which RSB’s management received very favorably.
- The management review templates were clearly designed
- the quality objectives as well as the risks and opportunities were completely re-evaluated or recorded and assessed. The renewals are excellently implemented.
- Since the last audit, a great improvement has been noted in terms of management system documentation.
- Competent staff and the high willingness of employees to continue their education.
The certificate has now been sent to us, which means that we have officially achieved ISO 9001 certification again.
Forecast
The validity of the certificate is now another 3 years. Between the external certification audits, an internal audit and a surveillance audit are carried out annually, in which the points defined for improvement from the previous audit are used and reviewed.
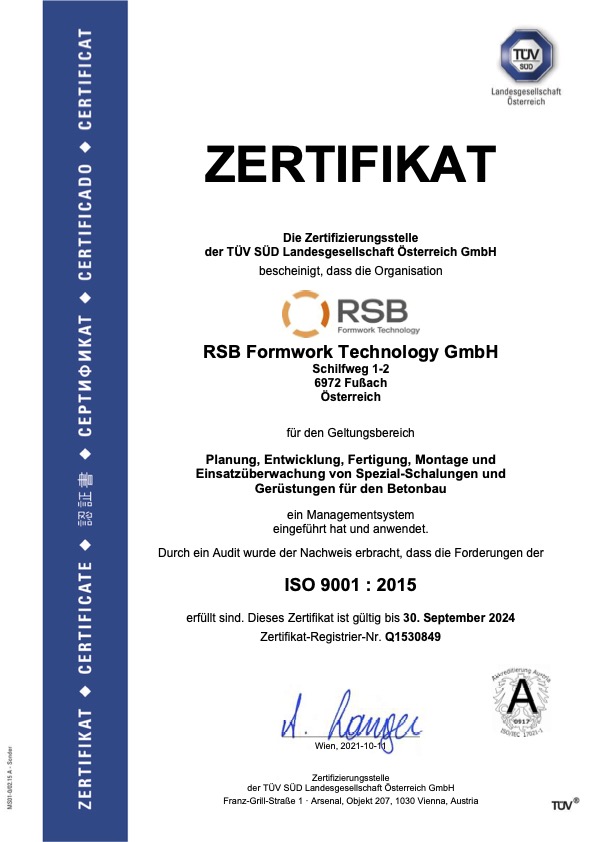
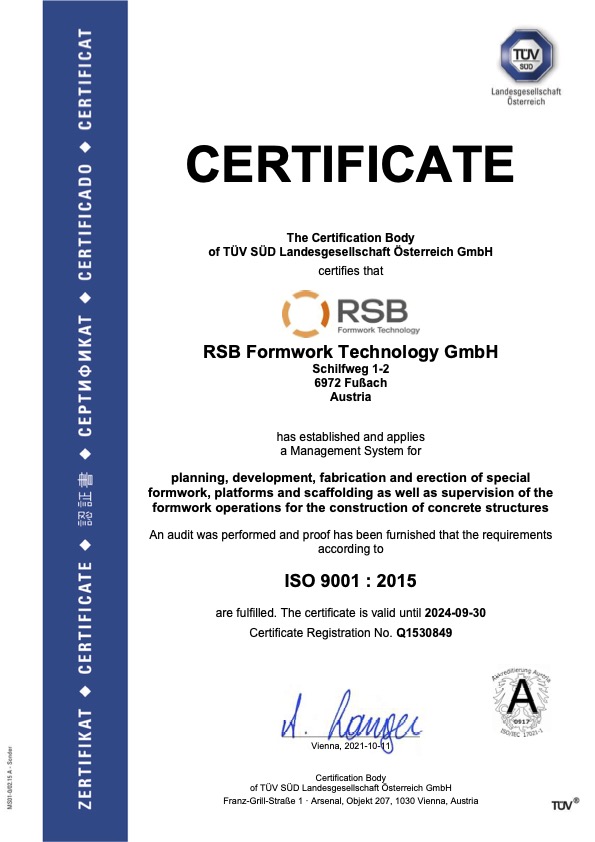
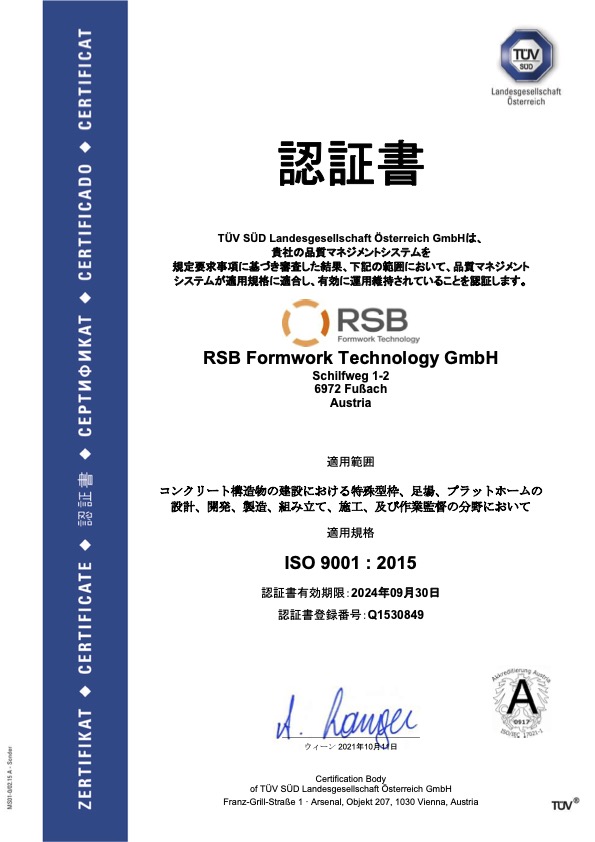
For RSB, it is still important to live the QMS (quality management system) and to continuously monitor the process indicators and implement measures for further development and improvement.
Summary
The effort required to obtain certification should not be underestimated. However, we have been able to accelerate the certification processes, as a very structured and revised quality management system is in place and an almost complete and constantly adapted documentation has been established over the years.
Furthermore, it is a great advantage that ISO 9001 puts customers and continuous improvement in the foreground, because both come together in the agile execution of projects. Obtaining and incorporating feedback from the customer, as well as the ongoing improvement of internal processes through retrospectives, are part of our standard project development process and did not have to be introduced.
(Excerpt from the report of the quality representative)